Charged EVs | Packaging second-life EV batteries into a plug-and-play energy storage system

Q&A with Smartville CEO and co-founder Antoni Tong
What do EV batteries have in common with athletes and politicians? Once they age out (or get voted out) of their positions, they have the opportunity to have a lucrative (and in the case of batteries, useful) second career. Repurposing depleted EV batteries for stationary storage applications will be a critical part of the future EV ecosystem.
However, there are complicating factors: battery packs come in many different sizes and form factors, and individual packs may retire from the road at different points in their lives, so their remaining capacity and overall health can vary greatly. How to assemble this motley mélange of used battery packs into a smoothly-functioning stationary storage system?
Smartville, which recently won a $5.9-million grant from the DOE, has developed a solution. The company’s new Smartville 360 ESS is a scalable second-life energy storage system that’s designed to incorporate battery packs from different manufacturers (currently, Tesla and Nissan), at varying levels of health, into one unified system. Smartville currently has a pilot project up and running at the University of California San Diego.
The company claims Smartville 360 offers the lowest embedded emissions and the best value per kilowatt-hour of any storage solution on the market. Smartville also hopes to differentiate itself from competitors by tailoring solutions to the needs of different types of customers.
CEO and co-founder Antoni Tong recently explained to Charged how the system works, and how the company procures batteries and prepares them for successful second careers.
Charged: Let’s start at step one. Tell me more about where you source the used batteries from.
Antoni Tong: We work with a variety of battery procurement partners across the value chain. For some battery procurement, we work with OEMs or battery service companies that are directly working with OEMs. For example, Nissan. They have manufacturing space in Tennessee, and they have repurposing programs through their North American headquarters, so we can source, procure and quality-control batteries directly from them.
We also work with Tesla Model 3 and Y packs, as they are US market leaders in EV sales. In terms of volume of battery capacity that’s out there, 60% to 70% are Tesla Model 3 and Y packs. Those we procure through auctions, insurance write-offs and third-party dismantlers.
Charged: If a car gets totaled, you might buy the battery pack on the salvage market?
Antoni Tong: Correct. The volumes actually are greater than we thought. We have seen at two of the major insurance auction sites, about 1% of the vehicles are coming through that pipeline in year one, and you will see about 15% of them before year 10. Those are fairly new and qualifiable batteries for reuse. Our market study indicates that over one GWh worth of batteries will be available for repurposing in the next three years.
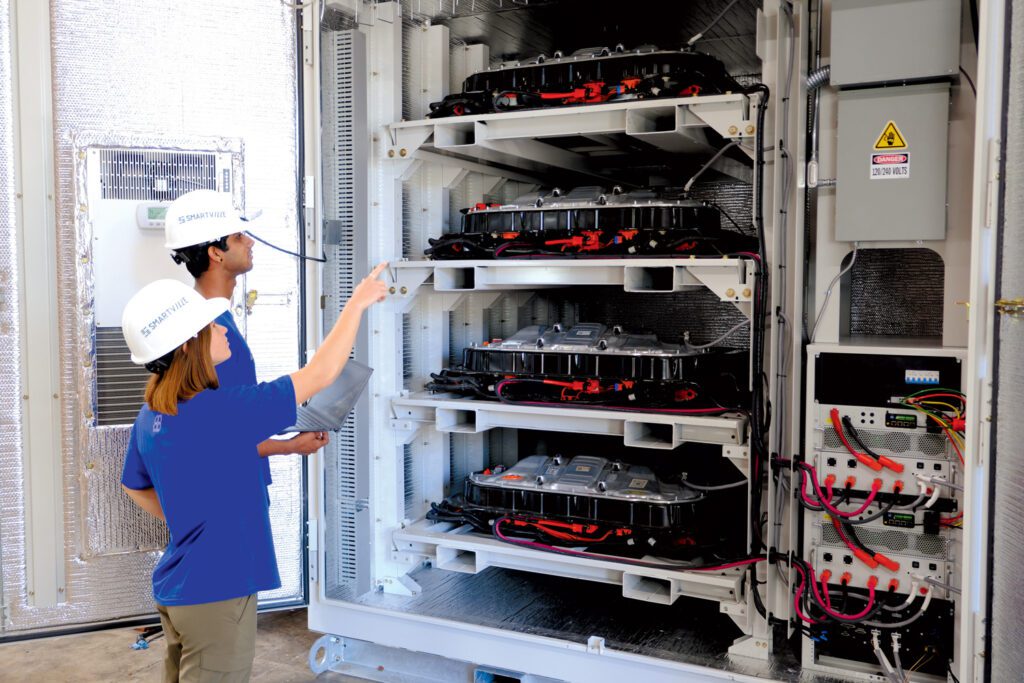
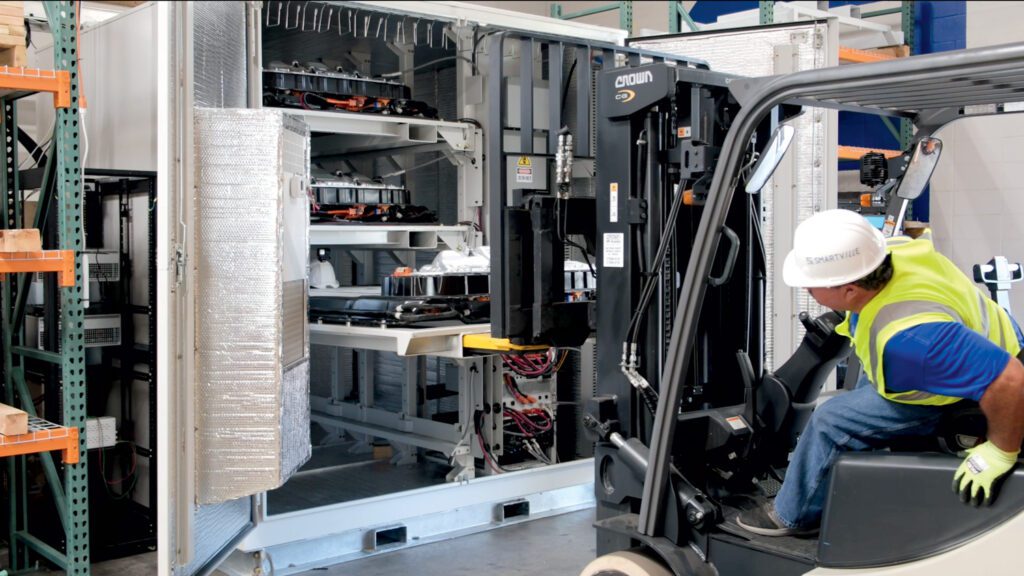
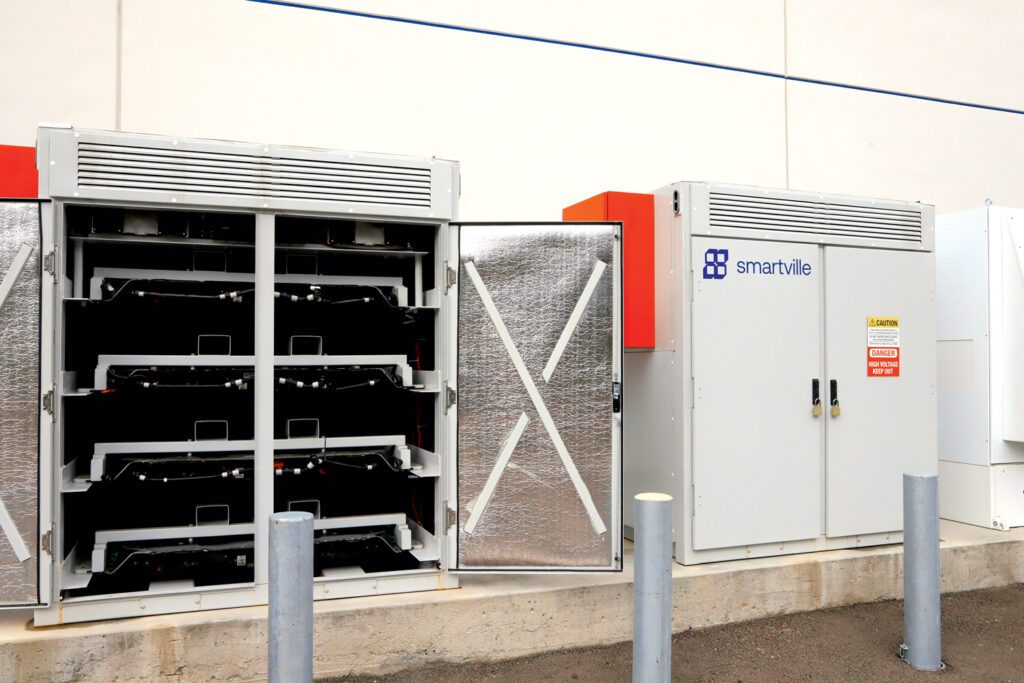
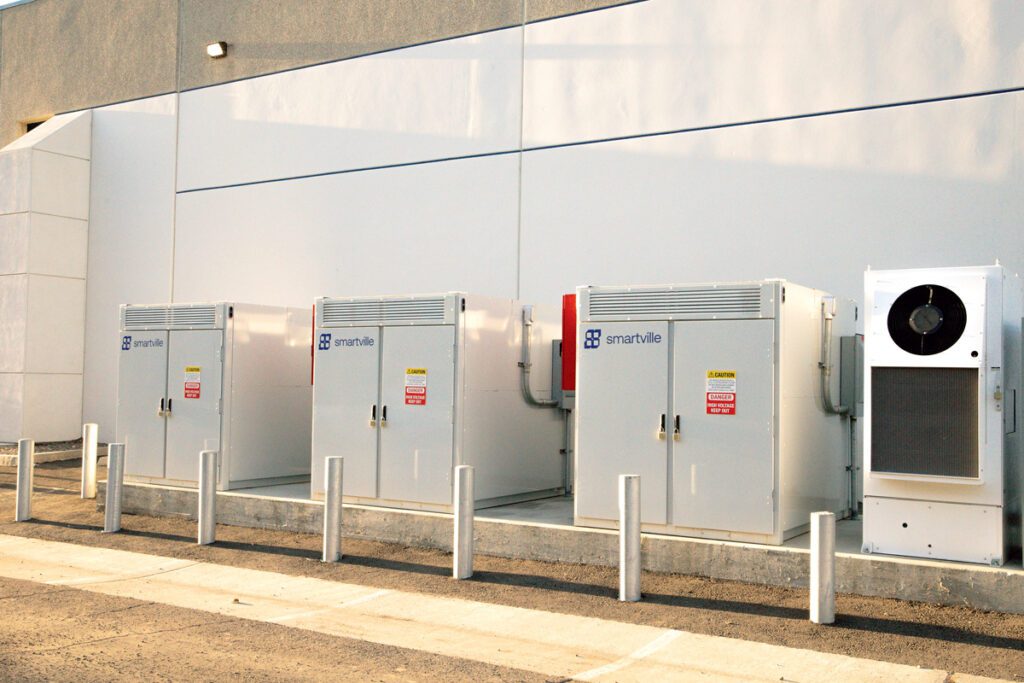
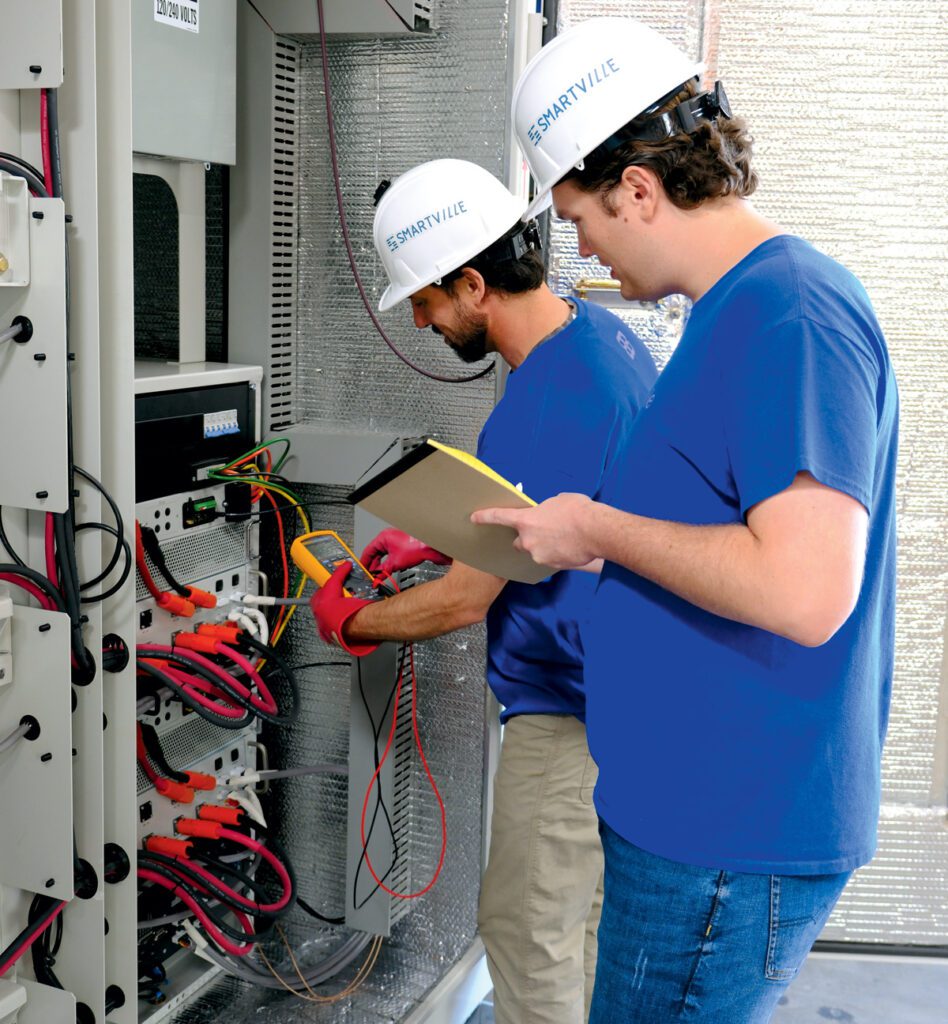
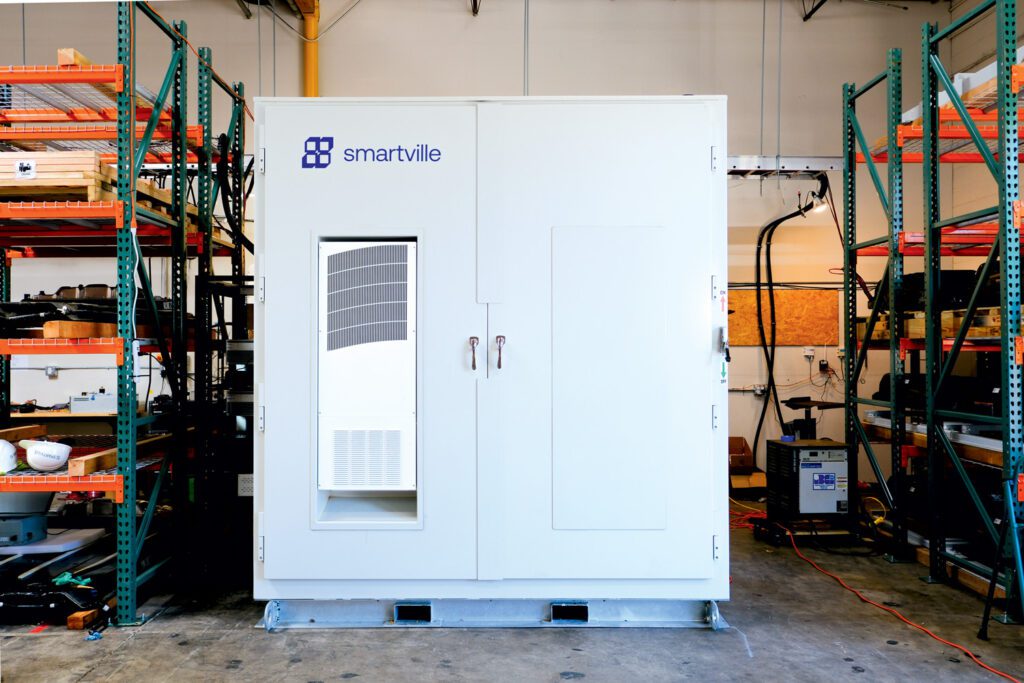
Charged: Your Smartvlle 360 platform is designed to use batteries from different vehicles—any battery chemistry, any type of battery, correct?
Antoni Tong: Yes, this is exactly the design-for-application approach we took to optimize the integration cost and competitiveness of our products, and reduce the risk of procurement. We are fairly confident that the products are agnostic with regard to OEMs and chemistries.
There’s only one nuance—typically, we design batteries by the class of voltage. Currently, more than 90% of vehicles are in the 400-volt class. We do start to see new trucks and buses using 800- or 1,200-class voltage, and that requires some retooling and update of power electronics on our end.
There are different schools of repurposing—the teardown model or the whole-pack repurposing model. Smartville does a whole-pack repurposing model.
Charged: What do you physically have to do with a pack to install it into your device? Surely you don’t just take the whole battery pack and stick it in the cabinet?
Antoni Tong: That’s exactly what we do. Let me give you some reasons. There are different schools of repurposing—the teardown model or the whole-pack repurposing model. Smartville does a whole-pack repurposing model.
There are business models in Asia and Europe doing teardown, but there are two reasons that this is going to be exceedingly challenging. One is the economics. In this market space, to do this requires high labor costs for reintegration. You’re also tampering with a perfectly sealed and engineered pack to rebuild a system that introduces new components and controls, which may mix in a manufacturing defect.
The second reason is the trend of how battery packs are being engineered. You are seeing bigger form-factor modules, something like cell-to-pack design, which make the pack almost indestructible, so the pathway for the teardown model almost doesn’t exist. For example, Tesla Models 3 and Y, and other large-format battery packs that we are starting to see in the market.
For those reasons, we’re trying to repurpose directly on the pack level. However, I should have prefaced, it’s not directly sticking the pack into the Smartville 360. We do qualification, we do cooling line integrations, we do quality checks, not only on the batteries but also on the critical parts within the pack. That includes the BMS, communications, cooling lines, seals, isolation detections, contact qualities. So, all that we’re going to be reusing outside of the battery will be qualified before we integrate them.
Charged: Tell me more about the qualification that you do on these battery packs.
Antoni Tong: Qualification is extremely important for our business model, and we hope to build a differentiating approach in that space.
Qualification is extremely important for our business model, and we hope to build a differentiating approach in that space.
What we do often starts even before we touch the batteries. We work with service providers, dismantlers, some of them even before the batteries come off the vehicles. We provide them with hardware and protocols so they are able to do initial sniffing of the batteries—taking pictures, reading manufacturing marks, reading VINs. We also have a device that can read CAN buses on the BMS to get odometer readings, mileage, accumulative cycles, so we can draw a map of the rough category of fitness of those batteries.
Once we determine some of the batteries are good, and get them to our factory, then we will conduct the testing we call “application-appropriate.” Because when they were in the vehicles, all the calibration, all the readings, all the BMS were reporting how the batteries operated in the vehicle. We test them on their quality for energy storage applications. We recalibrate their state of health and their state of charge, and then we prep them for integration. That procedure builds up a strong body of data intelligence that we are able to use to predict and guarantee performance.
Charged: Within the Smartville 360, you’ve got to connect the communication lines to the BMS, you’ve got to connect the coolant lines, and all those connections must be different for every different pack, right?
Antoni Tong: This is one of the unique toolings we had to do. The form factor fits the majority of the EV packs. And within each Smartville 360, we use the same type of battery—not only the same models but also very close model years. Every time we become compatible with a new type of battery pack, the first thing we do is retool the cables and retool the communication connections. But we find this to be largely similar, and we have a cable consultant and suppliers that are familiar with a lot of those retoolings in the automotive space.
Charged: So you don’t mix and match packs within a single Smartville 360 unit, but each different unit could be using different types of packs.
Antoni Tong: Correct.
Charged: You describe the Smartville 360 as a plug-and-play device. How does a customer connect it into their electrical service for peak shaving, backup power or other applications?
Antoni Tong: Our system can be configured for both DC and AC couplings. For the AC coupling, it comes with the inverter pre-integrated and fully turn-key. Our EMS system, despite our capability to work with batteries with different types and health, will coordinate the lower-level control so the customer will only see one unit of batteries to dispatch. A project developer will then take our EMS control interface and incorporate it with a larger site-level controller, which includes other energy components such as renewables, loads, grid-metering and switches.
The EMS is what they use to dispatch our ESS. For storage, it depends on applications. There are many, many different controls you can do. You mentioned a few: peak shaving, that’s looking at the time-of-use price; demand reduction. It’s more complicated looking at what’s the penalizing tier of the local utility. So, all those are different case-by-case situations.
Charged: There must be a software product that goes along with it. Is that something that you provide or can it work with different systems?
Antoni Tong: Both. Our systems come with the EMS that allows the integrator to dispatch the batteries. We also can be compatible with other more powerful EMS systems that the customer might use.
Charged: I guess second-life battery technology has come a long way in the 10 years since you began in the industry. What are some of the improvements and innovations that have happened?
Antoni Tong: In the past 10 years there have been a lot of pilots and trials, often OEM-initiated, typically working with developers or integrators to do demonstration projects.
Over the last couple of years, we have seen growth in the volume of batteries, the procurement model being further diversified, and a lot of companies working on different batteries. We are starting to see the emergence of solutions really targeting a competitive business model in the stationary storage space. Depending on the market sector they’re focusing on, the price structure might be different. But this is still in a very early stage.
Charged: What are some of the potential customers, and how do their needs differ?
Antoni Tong: Different companies are focusing on different customer sectors. Smartville today is focusing on about 100 kilowatt-hours to multi-megawatt-hours of installation as a market entry. We are targeting systems for commercial and industrial customers, or a leg up to a small grid-integrated level, but not like a gigawatt level of storage yet, as those applications require much larger manufacturing scales and financing vehicles than we are capable of today.
Charged: Smartville was founded in 2019. What stage in your development are you at? Are you still working on pilots or do you have some actual customer installations up and running?
Antoni Tong: So far, we are at the scaling point. Our first pilot-level product is Smartville 360, and right now, we are at iteration two. With iteration one, we had one installation done last year as a pilot. It’s subsidized by California Energy Commission funding.
We have four concurrent pilots ongoing right now. Smartville 360 version two is geared towards certification under the UL 9540 framework and is targeting low-rate production. With that product, we are doing our first commercial delivery to a utility company. We are hoping to showcase our products and underlying solutions in September at the RE+ Convention. We also have a couple of utility, commercial and auto OEM customers in the pipeline.
Charged: What do the auto OEMs use stationary storage for?
Antoni Tong: Some of them want a proof of concept on their batteries. They have incentives to see cost differences, should policy come that makes them responsible for battery packs that are in their vehicles or creating an internal application ecosystem for their battery packs.
Charged: The OEMs think there might be regulation in the future that will require them to support second-life batteries?
Antoni Tong:Generally, OEMs don’t want to comply unless there is a strong financial incentive. What I see is not only the risk of future policies, but also other financial incentives. Because nowadays, battery pack chemistries are moving toward low-cost, low-supply-risk raw materials, such as shifting from NCM to iron phosphate. The OEMs might see little to negative value in recycling only, meaning that they have more costs on their hands for end-of-life batteries. So hopefully, it’s a mix of policy push and the financial incentive to drive to a reuse and recycle model.
Nowadays, battery pack chemistries are moving toward low-cost, low-supply-risk raw materials, such as shifting from NCM to iron phosphate. The OEMs might see little to negative value in recycling only.
Charged: So recycling is in some cases not economically viable? How does that relate to second-life applications?
Antoni Tong: We see challenges on the profit side on the battery materials. Maybe two years ago during the height of COVID, battery raw materials could fetch high prices, but the price has been down by more than 50% since COVID subsided.
We also see different profit opportunities for different chemistries. The earlier batteries with high nickel, manganese and cobalt content fetch a better price, but batteries are not made this way nowadays. Very low nickel and cobalt contents today. The iron phosphate cells, they are basically iron and rust and some lithium. Those actually carry a cost to the end owner. It’s not a problem for OEMs today because they are not responsible for those packs. But once they do become liable for those costs, that’s a great financial incentive to find a responsible yet cost-effective end-of-life solution. And I hope at that time, reuse becomes a solution before recycling.
When we talk to collaborators and potential customers, we always say our business model is not in competition with recycling. We are in a complementary position with recycling, because we and the recycling entities are using very similar processes of logistics, shipping and procurement. The batteries have to come out of the vehicles, have to be sorted, have to be transported. But if we can pick the batteries that are usable for us, the cost to the recycler for procuring the rejected batteries will be lower. At the same time, when we triage large quantities of batteries for repurposing, we make it easier for those end-of-life batteries eventually to get to the door of the recycling plant.
Charged: Tell me about the future of sourcing packs. When do you think you’re going to see a lot of actual end-of-life battery packs coming on the market?
Antoni Tong: This is a very good question. Our retaining rate, which means the salvage rate on the vehicle side, is also driven by the significant growth of the EV space. We see north of gigawatt-hours of used batteries available as early as 2027. That’s a significant amount, much larger than our target procurement model within Smartville’s business objective.
We see north of gigawatt-hours of used batteries available as early as 2027…much larger than our target procurement model within Smartville’s business objective.
But there’s a nuance as to whether they are really end-of-life. There is no clear line that a battery used beyond 80% remaining capacity is true end-of-life. There will be a spectrum, and we continue to work with batteries of all ages. Some came right off the factory floor and got into accidents. Some people are driving old Nissans down to only 40 miles of range, and we have those batteries at our factory as well. The key here is to establish good battery data analytics to provide the prescribed service life and performance in our integrated product.
Charged: My LEAF is down to 80 miles of range, but it gets me where I need to go, so you won’t get that battery pack for a long time.
Antoni Tong: Right. But to add to that, a lot of our motivation is also coming from sustainability objectives. Just to throw a number out there, a new EV needs to drive about 13,500 miles to equal the embedded carbon emissions compared to a gasoline car, according to Reuters. Which means if you have a vehicle that gets totaled before year three, year five, that’s a more polluting car than gasoline. [Editor’s note: There are widely varying estimates as to the mileage required to cancel out an EV’s “carbon backpack.”]
You have tons of battery assets out there that are being ground down for material. Alternatively, if we can pick them up and bring them a second life, we can fulfill their carbon emission reduction goals.
Charged: In California they’re introducing some incentives for stationary storage, and I think the IRA and the BIL address this too. Are there state and federal incentives that you’re able to tap into?
Antoni Tong: There are strong incentives for stationary storage in the IRA, but there are wrinkles for the line of business we do. For example, as the IRC section 48 Energy Investment Credit stands today, second-life batteries were left out of the technology candidates to receive project-wide tax incentives. However, we have a very strong case that this is a shifting of application—it’s a battery that’s not purposely for stationary storage and we, through engineering, developed a new line of product. I think we can make a case for the product to be qualified—but there is risk there.
And if you are qualified for a certain percentage of domestic manufacturing, you qualify for additional tax rebates. Which, interestingly for Smartville, our products have very, very high percentages of domestic content. Thanks to our low-risk supply chain and localized manufacturing practice, our enclosures, our power electronics, interface stages, and the batteries, are sourced or manufactured in the US, as opposed to other energy storage products that you typically see—batteries are largely coming from overseas.
This is one of the things that the battery circularity industry as a community is investigating. One possibility is that we submit projects for a private letter ruling (PLR) on qualifying under the IRA. We also look to see campaigning and lobbying efforts that could qualify these products for tax incentives. After all, achieving scalable repurposing, in our opinion, is a key step to achieving a sustainable domestic lithium-ion battery supply chain.
This article appeared in Issue 65: July-September 2023 – Subscribe now.