Charged EVs | MP Materials has an ambitious US rare earth supply chain strategy to fuel EV innovation

- Permanent magnet motors are dominant in the EV industry, due to their superior efficiency. The majority of EV traction motors use rare earth magnets.
- MP Materials claims to be the only scaled producer of rare earth materials in the Western Hemisphere. Over 90% of the world’s rare earth magnets are produced in China.
- There are three stages in the rare earth magnet production process: mining; separating and purifying the elements; and transforming the elements into metal alloys and magnets. MP Materials aims to establish all three stages in the US.
- Recycling rare earth materials is vital to the cost-competitiveness of magnet manufacturing. In the process of producing a magnet, up to 30% of the material can end up as scrap, and a producer must have the ability to recycle that material.
Q&A with MP Materials’ Matt Sloustcher.
There’s much hand-wringing in the press these days about battery raw materials such as lithium, cobalt and nickel. However, save some of your anxiety for rare earth materials. These elements (which are not particularly rare, but seemed so to the scientists who named them back in the 18th century) are critical components of motors, and like the strategic materials used in batteries, they tend to come from faraway countries with problematic environmental and/or political profiles.
Establishing extraction and processing of rare earths closer to the places where automotive components are made is a high priority, but it’s not something that can be rushed. By most accounts, the process of bringing a new mine into operation can take anywhere from five to ten years.
MP Materials is in the enviable position of having a mine and processing facility already up and running in California, and it has big ambitions. The company has won some $45 million in contracts with the US Defense Department to expand its heavy rare earth element (HREE) processing capacity. What’s more, the company is developing a facility in Fort Worth, Texas where it plans to manufacture alloys and magnets from Mountain Pass materials. And it has customers. In 2022, MP signed a long-term agreement with GM to supply US-sourced and manufactured rare earth materials, alloys and magnets.
MORE: A closer look at rare earth permanent magnets
Charged spoke with Matt Sloustcher, MP Materials Senior Vice President of Communications and Policy, about the importance of rare earths and how his company is building a complete rare earth supply chain here in the US.
Charged: I know that rare earths are used for a lot of high-tech applications, but just narrowing things down to EVs, are they used in any other EV components besides magnets?
Matt Sloustcher: The key application is magnets for traction motors, but rare earths are found throughout all vehicles, in things like speakers, sensors, and electrical devices like power mirrors and seats. So even in conventional ICE vehicles, you do find a good amount of rare earths and magnets.
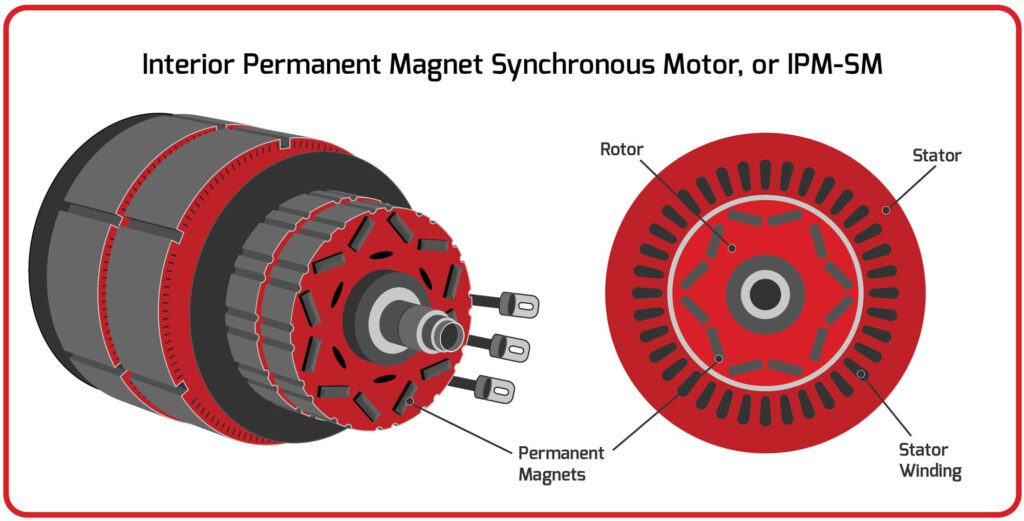
Electric motors work on the principle of electromagnetic motion. The key enabling technology is magnets, and the preponderance of those magnets are rare earth magnets. Rare earth magnets are the most efficient, and they have the highest power density of any kind of magnet. Something like 90% of the drive motors in electrified vehicles are powered by rare earth magnets. There are other types of motor technologies, namely induction motors, but permanent magnet motors are dominant because they’re the most efficient.
Something like 90% of the drive motors in electrified vehicles are powered by rare earth magnets. There are other types of motor technologies, namely induction motors, but permanent magnet motors are dominant because they’re the most efficient.
Charged: Tell me a bit about the global market for rare earths. How many companies are providing rare earths from within the US or Europe?
Matt Sloustcher: MP Materials is the only scaled producer of rare earth materials in the Western Hemisphere. And the way to think about this supply chain is that there are three stages in the production process. The first stage is extraction and beneficiation—essentially mining the material and then producing a concentrate. The second stage is separation and refining—taking a mixed bag of rare earths (there are 17 rare earths in total), then separating and purifying the target elements. The third stage is transforming the purified elements into metal, alloys and ultimately magnets.
When you look at the global supply chain for rare earths across all three stages, Asia is dominant, and China in particular. Over 90% of the world’s rare earth magnets are produced in China, and there is virtually no scale capacity in North America today to produce rare earth magnets.
Charged: New laws in the US and Europe are encouraging domestic sources of supply, so that would seem to be a big opportunity for you—but maybe the incentives for domestic production aren’t as important on the motor side as on the battery side.
Matt Sloustcher: If you read the EV Tax Credit legislation, the sourcing restrictions on critical minerals are limited to the battery system. Rare earths are used in nickel metal hydride batteries, but not really to a significant extent in lithium-ion batteries. However, the IRA does provide a production tax credit for critical mineral production, which will benefit our operation.
Through Section 45X [the Advanced Manufacturing Production Credit] and other policies, the IRA will help level the playing field for domestic materials producers. Advancing bipartisan legislation such as H.R. 5033 and S4680 [which would establish a new tax credit for the domestic production of rare earth magnets] would accelerate the onshoring of domestic magnet manufacturing.
However, I think there’s a tremendous push to onshore on the part of manufacturers, simply for supply chain resiliency. Today, there is a single point of failure in the supply chain for rare earth materials. I think domestic manufacturers of components and vehicles are searching for more diversity, more resiliency and more sustainability in the supply chain. And a real testament to that is the fact that we are building a fully-integrated magnetics manufacturing facility in Fort Worth, Texas, and we have a definitive agreement with GM to supply them with rare earth magnets to support their North American EV production.
Over 90% of the world’s rare earth magnets are produced in China, and there is virtually no scale capacity in North America today to produce rare earth magnets. There’s a tremendous push to onshore on the part of manufacturers, simply for supply chain resiliency.
Charged: Of course, sustainability is another good reason to build domestic supply chains. What steps have you taken to limit the footprint of your mining and processing?
Matt Sloustcher: We believe, without question, that our Mountain Pass mine and processing facility is the world’s most environmentally-responsible source of rare earth production.
Mountain Pass is a zero-discharge facility. We have a dry tailings process. If you look at pictures of most mines around the world, you’ll see big tailings ponds, where essentially the waste material that is in the liquid settles. And tailings ponds, if they’re not carefully managed, can result in groundwater contamination. In some developing countries, there have been dam failures which have endangered communities.
At Mountain Pass, we take the water out of the tailings and we recycle the water. In our current operation, around 95% of the water we use at Mountain Pass for processing is recycled in a closed loop. Then we return dry material to ground in a lined impoundment. So, we take the material out of the ground in a dry state, we use water in the processing and concentration process, and then we de-water the tailings and put dry material back to ground.
This is exceptionally rare in mining—something like 5% of the new mining operations since 1970 have a dry tailings process. We are the only site in the global rare earth industry to employ a dry tailings process, and the environmental benefits from that are really significant.
Another important factor is that Mountain Pass is a co-located mine and processing facility. It’s fully integrated, so we’re not mining the material and concentrating it in one place and then shipping it vast distances for further refining. For us, that provides environmental benefits, as well as overall efficiency and cost benefits.
We believe, without question, that our Mountain Pass mine and processing facility is the world’s most environmentally-responsible source of rare earth production.
Charged: Tell me about the new plant that you’re building in Texas.
Matt Sloustcher: Our mission as a company is to restore the full rare earth supply chain to the United States, including all three of those stages we talked about: mining; processing; and ultimately, the transformation into metals, alloys and magnets. You cannot take a refined rare material and put it inside an electric motor. You have to take that material and make metals, alloys, and then ultimately the finished magnets.
So, our strategy as a business is to integrate vertically. From a supply chain resiliency point of view, this is really important. Also from an energy security point of view. We believe it’s imperative that the US has the capability to command at scale all pieces of the rare earth supply chain, from mining all the way through to magnet manufacturing, and then recycling. So, that is what we are doing—vertically integrating, and it combines our operations at Mountain Pass, which accomplishes the first two stages, and then this magnetics facility that we’re building in Fort Worth, Texas.
We broke ground at the Fort Worth site in April of 2022. We’ve completed the building shell, and so now a lot of the work is going on inside the building. Our goal is to begin delivering products this year.
This facility will be our North American magnetics headquarters, not just production, but also engineering. We’re building a world-class engineering team because we think there’s a real opportunity here to advance the state of the art with respect to design and manufacturing of magnets. And that’s how we intend to develop a competitive advantage.
Our mission as a company is to restore the full rare earth supply chain to the United States, including all three of those stages we talked about: mining; processing; and ultimately, the transformation into metals, alloys and magnets.
Charged: What about your deal with GM? Are you going to be supplying them with magnets made in Texas?
Matt Sloustcher: It is a definitive supply agreement to supply GM with magnetic alloy and finished magnets to support their North American production. The deal specifically is for more than 12 models on their Ultium platform. The materials that go into those products will be sourced at Mountain Pass, so what we are providing is a fully integrated solution, from the point of extraction all the way to the point of magnet manufacturing.
Charged: When you’re supplying magnets, how specific are the customer requirements? For example, with this GM deal, do you supply different magnets for different car models, or…?
Matt Sloustcher: Magnets are engineered components, they are not commodities in any way, shape or form. When we talk about neo magnets, which are the dominant form of magnets used in traction motors, they’re made with the rare compound neodymium praseodymium, NdPr. There are over 50 grades of neo magnets, and they can come in all shapes, sizes or form factors.
Different automakers have different strategies concerning the underlying materials in their rare magnets, and the operating conditions. The development of a magnet spec is very closely aligned to the development of an electric motor and how it’s going to function. The way to think about it is that they’re engineered specific to the use case—there are some commonalities, but every automaker’s got a different approach to the motors and magnets that it uses within its platforms.
Charged: Do you have any other customers that you can talk about?
Matt Sloustcher: What I’ll say is that the deal with GM is not exclusive. They are our foundational automotive customer, but we are eager to serve customers globally out of our magnetics business. This is our first magnetics facility, but our goal is to further scale our magnetics business from here.
I think it’s worth noting that Mountain Pass is a very large source of production globally. In 2021, we supplied around 15% of global rare earth content. We believe it’s the second-largest single source of rare earth production globally. When we fully commission and scale the refining and processing operation at Mountain Pass, we’ll produce over 6,000 tons of NdPr annually.
That’s sufficient to produce magnets that can power 6 to 10 million EV traction motors. This first magnetics facility we’re building in Texas will consume less than 10% of the NdPr output at run rate that we will be making at Mountain Pass, so there is room to scale from here and build additional magnetics capability. The Texas facility, it’s scalable, so we might scale up, but currently, it has an annual capacity to produce magnets that can power around 500,000 EV motors.
Charged: You’re selling the raw materials right now, and you will be selling the finished alloys and magnets. So you’ll be serving two different sets of customers, right?
Matt Sloustcher: That’s correct. We have a materials business and we have a magnetics business. We recently announced a deal to supply materials to the Japanese market through Sumitomo Corporation as our distributor. And so we will be selling materials and magnetic products concurrently.
Concerning the Sumitomo deal, the largest market where neo magnets are produced outside of China is Japan. So Japan does have capacity to manufacture magnets today, and we believe we can provide some diversity and resiliency to that market, which is really important for Japan’s manufacturing sector, by supplying materials that are produced out of the US.
Charged: As far as the materials business, who are the customers? Are they motor makers or are they further upstream?
Matt Sloustcher: Essentially, magnetic companies are the customers with respect to NdPr (this gets complex). But we will produce other rare earths in our materials business that are used for other purposes. For example, lanthanum products are used as FCC [fluid catalytic cracking] catalysts for the production of jet fuel. Cerium products can be used for water treatment. So we will supply materials for non-EV-specific or motor- or magnet-specific applications as well.
Having the ability to recycle rare earth materials is vital to the cost-competitiveness of magnet manufacturing. As much as 20% or 30% of the material that goes into the process might come out as scrap. You must have the ability to recycle that material.
Charged: We hear a lot about supply chain shortages of materials. Where does recycling fit into that picture?
Matt Sloustcher: I think long-term, the importance of recycling is obvious from a sustainability point of view, and also a natural resource preservation point of view. But in the near term, having the ability to recycle rare earth materials is vital to the cost-competitiveness of magnet manufacturing. When you produce a rare earth magnet, you can imagine that at the latter stages of the process, there’s cutting involved, there’s shaping involved, and that produces scrap.
As much as 20% or 30% of the material that goes into the process might come out as scrap. There might be an instance in which you take a square block and you cut it into a circular shape, so what do you do with the four corners? You must have the ability to recycle that material. MP Materials, we believe, is positioned to be a leading global company with respect to rare earth recycling.
We are now conducting some really exciting pilot work, involving large commercial entities, to demonstrate that this is technologically feasible. We have a unique competitive advantage because we’re developing a fully-integrated supply chain from the point of extraction to the point of magnets, so our engineers are able to ascertain where is the best part of the process to reinsert that material in the closed loop. Is it all the way back at the point of refining? Do you separate those elements back and purify them? Or is it somewhere in the magnet manufacturing process—is that more efficient? We have that flexibility because we’re developing the full flow sheet, all the way from mine to magnet manufacturer, and that’s unique.